स्क्रीनिंग संयंत्रों का रखरखाव और समस्या निवारण
ब्लॉग
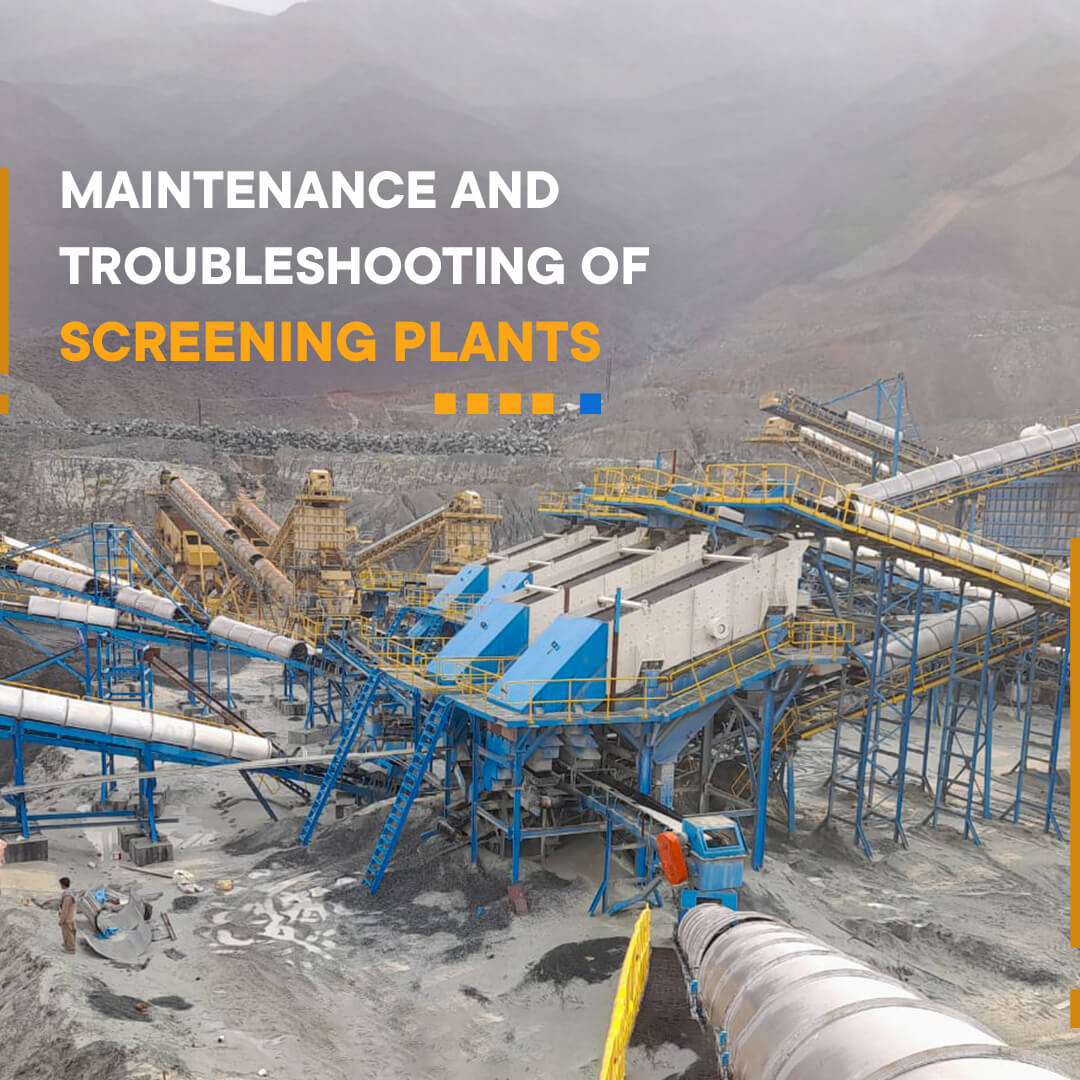
स्क्रीनिंग प्लांट खनन, निर्माण और रीसाइक्लिंग जैसे विभिन्न उद्योगों में आवश्यक घटक हैं, क्योंकि वे सामग्रियों के पृथक्करण और प्रसंस्करण में महत्वपूर्ण भूमिका निभाते हैं। हालाँकि, इष्टतम प्रदर्शन और लंबी सेवा जीवन सुनिश्चित करने के लिए उचित रखरखाव और समस्या निवारण आवश्यक है। इस ब्लॉग पोस्ट में Puzzolana.com स्क्रीनिंग प्लांट की प्रभावशीलता और दक्षता को अधिकतम करने के लिए रखरखाव और समस्या निवारण के महत्व पर चर्चा करता है।
प्रमुख रखरखाव और समस्या निवारण प्रथाओं को समझकर, ऑपरेटर सामान्य समस्याओं का समाधान कर सकते हैं, डाउनटाइम को कम कर सकते हैं और स्क्रीनिंग सुविधा के प्रदर्शन को अनुकूलित कर सकते हैं।
नियमित निरीक्षण एवं सफाई
नियमित निरीक्षण और सफाई संयंत्र के रखरखाव के प्रमुख घटक हैं। ऑपरेटरों को नियमित रूप से स्क्रीन, बेल्ट, रोलर्स और अन्य घटकों की टूट-फूट, क्षति या सामग्री निर्माण के संकेतों की जांच करनी चाहिए। यह निरीक्षण संभावित समस्याओं की पहचान करने में मदद करता है और समय पर रखरखाव और मरम्मत की अनुमति देता है। सामग्री की रुकावट को रोकने और स्क्रीन की चमक को कम करने के लिए सफाई आवश्यक है। स्क्रीनिंग सुविधा के प्रकार के आधार पर, सफाई के तरीकों में मलबा हटाने और सामग्री की निर्बाध आवाजाही सुनिश्चित करने के लिए ब्रश करना, छिड़काव करना या हवा की सफाई करना शामिल हो सकता है। नियमित सफाई न केवल इष्टतम स्क्रीनिंग प्रदर्शन को बनाए रखती है बल्कि उपकरण के जीवन को भी बढ़ाती है।
घटकों का स्नेहन और प्रतिस्थापन
स्क्रीनिंग उपकरणों के परेशानी मुक्त संचालन और दीर्घायु के लिए उचित स्नेहन महत्वपूर्ण है। बीयरिंग, गियर और अन्य चलती भागों को चिकनाई करते समय उपयोगकर्ताओं को निर्माता के निर्देशों और शेड्यूल का पालन करना चाहिए। नियमित स्नेहन घर्षण को रोकता है, घिसाव को कम करता है और घटक के टूटने के जोखिम को कम करता है। घटकों को बदलना रखरखाव का एक और महत्वपूर्ण हिस्सा है। इष्टतम स्क्रीनिंग प्रदर्शन बनाए रखने के लिए घिसे हुए कवर, बेल्ट और अन्य उपभोज्य भागों को तुरंत बदला जाना चाहिए। स्पेयर पार्ट्स को हाथ में रखने से डाउनटाइम को कम किया जा सकता है और संभावित उपकरण विफलताओं पर त्वरित प्रतिक्रिया सुनिश्चित की जा सकती है।
अंशांकन और समायोजन
स्क्रीनिंग दक्षता और सटीक परिणाम बनाए रखने के लिए स्क्रीनिंग संयंत्रों का नियमित समायोजन और अंशांकन आवश्यक है। उपयोगकर्ताओं को नियमित रूप से स्क्रीन झुकाव, गति और कंपन मापदंडों की जांच करनी चाहिए ताकि यह सुनिश्चित हो सके कि वे वांछित आवश्यकताओं को पूरा करते हैं। गलत समायोजन के परिणामस्वरूप सामग्री का पृथक्करण इष्टतम से कम हो सकता है और प्रदर्शन कम हो सकता है। इसके अलावा, संसाधित होने वाली सामग्री की विशेषताओं के अनुसार स्क्रीन सेटिंग्स को समायोजित करना महत्वपूर्ण है। स्क्रीन एपर्चर, आयाम और आवृत्ति की फ़ाइन-ट्यूनिंग स्क्रीनिंग प्रक्रिया को अनुकूलित कर सकती है और वांछित आकार के अंशों का कुशल पृथक्करण सुनिश्चित कर सकती है।
सामान्य समस्याओं का समाधान
स्क्रीनिंग संयंत्रों को सामान्य समस्याओं का सामना करना पड़ सकता है जिनकी प्रभावशीलता को बनाए रखने के लिए परेशानी की आवश्यकता होती है। स्क्रीन की चमक, सामग्री की गति, अत्यधिक कंपन और बेल्ट की गति जैसी समस्याएं स्क्रीनिंग प्रक्रिया की प्रभावशीलता में हस्तक्षेप कर सकती हैं। ऑपरेटरों को इन समस्याओं के मूल कारणों की पहचान करने और उचित समाधान तुरंत लागू करने के लिए समस्या निवारण तकनीकों से परिचित होना चाहिए। इसमें डिस्प्ले सेटिंग्स को समायोजित करना, घिसे हुए हिस्सों को साफ करना या बदलना, या यांत्रिक या विद्युत समस्याओं को ठीक करना शामिल हो सकता है।
निष्कर्ष
इष्टतम प्रदर्शन सुनिश्चित करने और डाउनटाइम को कम करने के लिए स्क्रीनिंग संयंत्रों के लिए उचित रखरखाव और समस्या निवारण महत्वपूर्ण है। नियमित निरीक्षण, सफाई, चिकनाई और घटकों का प्रतिस्थापन आवश्यक रखरखाव कार्य हैं। अंशांकन और समायोजन सटीक स्क्रीनिंग बनाए रखने में मदद करते हैं, जबकि शक्तिशाली समस्या निवारण उपयोगकर्ताओं को सामान्य समस्याओं को तुरंत हल करने की अनुमति देता है। रखरखाव और समस्या निवारण को प्राथमिकता देकर, ऑपरेटर स्क्रीनिंग संयंत्रों के जीवन को अधिकतम कर सकते हैं, स्क्रीनिंग दक्षता में सुधार कर सकते हैं और भारत में विभिन्न उद्योगों की समग्र उत्पादकता और सफलता में योगदान कर सकते हैं।
हमारी विस्तृत मशीनरी देखें
पुज़ोलाना के साथ, आपके पास क्षेत्र के सबसे प्रतिभाशाली पेशेवरों के साथ काम करने और हमारे विस्तारित वैश्विक पदचिह्न का हिस्सा बनने का मौका है। हम अपनी टीम में शामिल होने के लिए प्रेरित पेशेवरों की तलाश कर रहे हैं।