Keeping Machines Alive: Unveiling Puzzolana’s Story of Gearbox and Motor Maintenance
Blogs
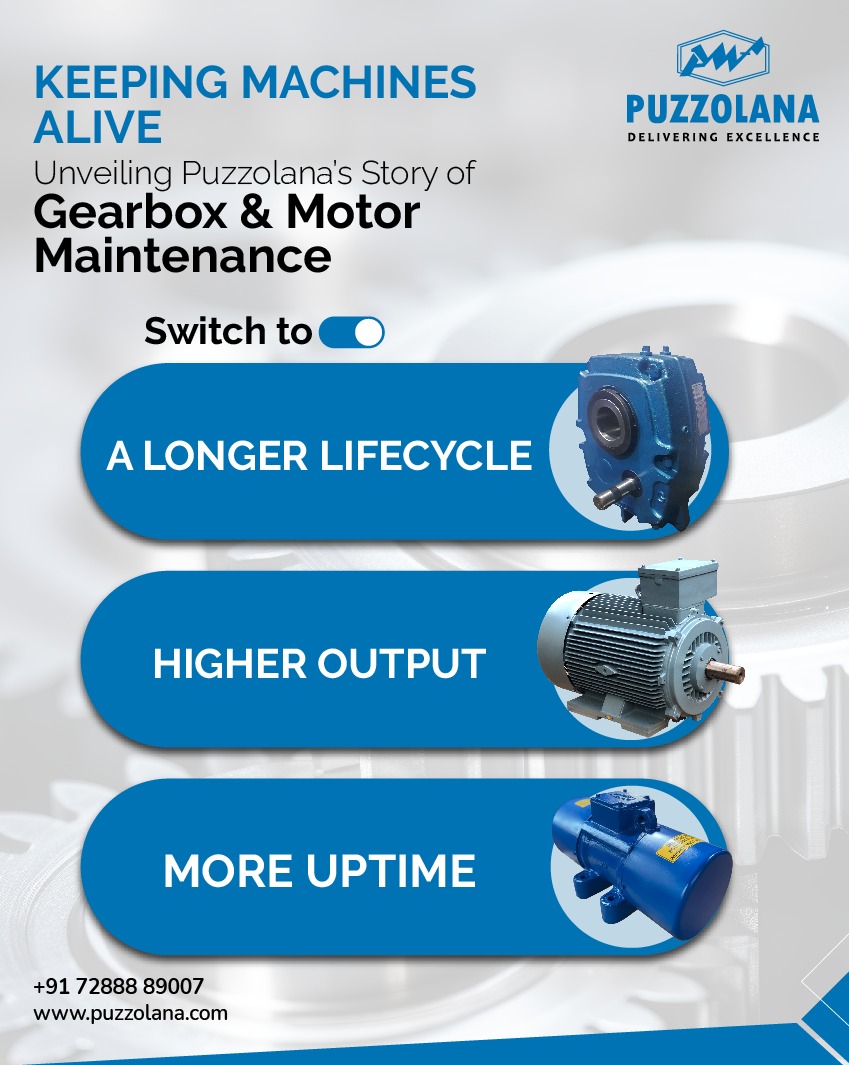
The sound of rock crushing is often the rhythm of progress — a measured pulse of industry and infrastructure coming to life. But what keeps that rhythm steady, day after day, in some of the most unforgiving environments on Earth? For Puzzolana, the answer has always started not with the stone, but with the soul of the machine — the gearboxes and motors that drive it.
This is the story of how Puzzolana learned, evolved, and engineered an entire philosophy around maintaining these critical components. Because for a machine to perform under pressure, its foundation must be unwavering.
The First Realization: Performance Begins Beneath the Surface
In the world of crushing, not all challenges arrive with alarms. Sometimes, performance tapers off quietly — no jams, no visible damage, just a gradual shift in output that doesn’t match expectations.
Often, the underlying cause lies beneath the surface: thermal stress, evolving site conditions, or wear patterns that don’t show until they’ve taken a toll. These are realities most plants encounter at some point — not due to neglect, but because crushing environments demand more than meets the eye.
That’s exactly why Puzzolana parts are engineered with foresight. From superior metallurgy to smart design that supports long-term reliability, our components are built to handle the unseen — so your operations stay one step ahead, always.
A Shift Towards Precision and Prevention
The first lesson was unmistakable: waiting for failure is not an option.
From that point forward, a new maintenance culture began. Gearbox and motor servicing transformed from reactive procedures into proactive strategies. Operators were trained to identify subtle signs — slight shifts in vibration, minor rises in temperature, faint acoustic changes. These weren’t just technical data points; they were warning signs — the machine’s early cries for attention.
Lubrication practices evolved. Earlier, standard intervals sufficed, but soon it became clear that high-load environments and extreme climates demanded smarter lubrication strategies. Lubricants became more than a necessity; they became protectors — preventing friction, reducing heat, and preserving internal integrity.
Thermal monitoring became a standard step. Infrared inspections began identifying stress zones long before they translated into visible failures. These innovations in predictive maintenance for industrial gearboxes added significant lifespan to components that once faced premature breakdown.
Lessons from Harsh Environments
From the crushing sites of southern India to the rugged quarries in the north, Puzzolana’s machines were tested by extremes — dust-heavy atmospheres, punishing heat, round-theclock loads. And each location taught something new.
One particular challenge at a high-output site revealed a pattern of recurring motor bearing failures. Investigations led to a surprising conclusion: shaft misalignment, often overlooked, was quietly degrading performance. It was a turning point. From then on, alignment tools — mechanical and laser — were introduced into the standard service protocols. Precision became the norm, not the exception.
Diagnostics, Data, and Long-Term Care
The next chapter in this journey arrived with digital insight. Where intuition once guided maintenance, diagnostics began to lead. Vibration analysis and oil sampling became regular tools — not just in labs, but in the field. These methods uncovered wear patterns, identified contaminations, and forecasted potential issues before they could disrupt operations.
Oil analysis, especially, became a cornerstone. Tracking viscosity shifts, metal particles, and fluid contamination levels offered a window into gearbox health — a predictive tool that helped plan overhauls rather than react to breakdowns.
But beyond the tools, it was the mindset that changed. Maintenance was no longer treated as a support function. Within Puzzolana’s engineering and operations teams, it became a shared responsibility — embedded into the design, integrated into the build, and carried into the field.
Engineered for Longevity, Designed for Reliability
Today, gearbox and motor maintenance is woven into every stage of a Puzzolana machine’s lifecycle. From initial assembly to site commissioning, every step is optimized for long-term care. Engineers factor in ease of access for servicing. Assemblers are trained to account for future overhauls. And technicians on-site operate with deep technical knowledge and diagnostic precision.
This isn’t about routine servicing anymore — it’s about sustaining excellence. It’s about machines that don’t just work hard, but work smart, with minimal downtime and maximum lifespan.
The Heart of Crushing Power
Gearboxes and motors may not be the most visible parts of a crushing plant, but they are undoubtedly the most vital. They endure the pressure, drive the output, and absorb the stress — quietly powering the performance customers rely on.
At Puzzolana, maintaining these components isn’t just engineering discipline — it’s a commitment to quality, reliability, and progress. Because in the world of crushing and screening, true performance isn’t just measured in output. It’s measured in uptime, endurance, and trust built over time.
And that’s what Puzzolana continues to deliver — one well-maintained machine at a time.
View our expansive machinery
With Puzzolana, you have the chance to work with the brightest professionals in the field and be a part of our expanding global footprint. We are looking for motivated professionals to join our team.