Maintenance and Troubleshooting of Screening Plants
Blogs
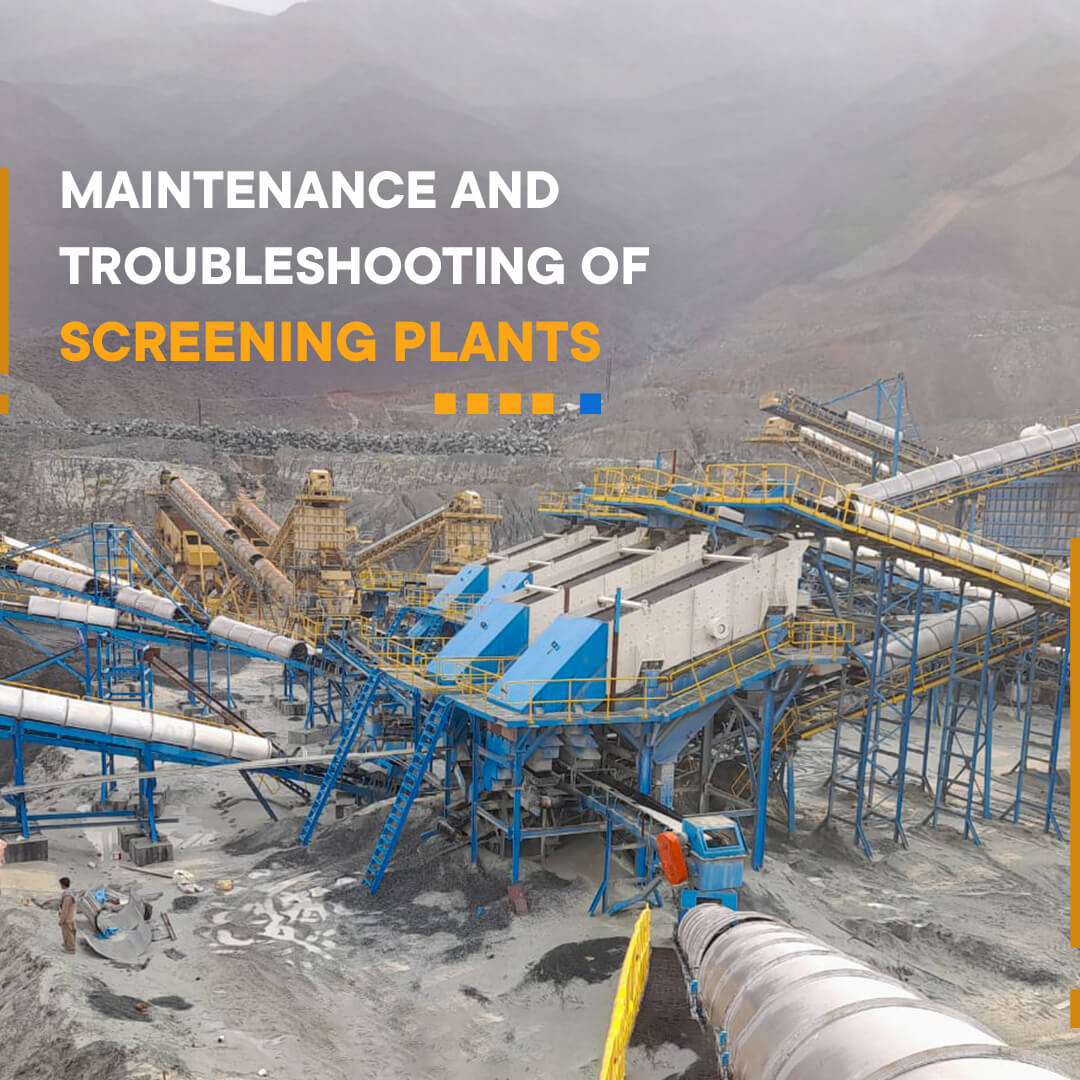
Screening plants are essential components in various industries such as mining, construction and recycling, as they play a key role in the separation and processing of materials. However, proper maintenance and troubleshooting are necessary to ensure optimal performance and long service life. In this blog post Puzzolana.com discusses the importance of maintenance and troubleshooting to maximise the effectiveness and efficiency of screening plants.
Understanding key maintenance and troubleshooting practices, operators can address common problems, minimise downtime, and optimise screening facility performance.
Regular Inspection and Cleaning
Regular inspection and cleaning are key components of plant maintenance. Operators should regularly check screens, belts, rollers and other components for signs of wear, damage or material build-up. This inspection helps identify potential problems and allows for timely maintenance and repairs. Cleaning is essential to prevent material clogging and reduce screen glare. Depending on the type of screening facility, cleaning methods may include brushing, spraying, or air cleaning to remove debris and ensure unfettered material movement. Regular cleaning not only maintains optimal screening performance but also extends the life of the equipment.
Lubrication and Replacement of Components
Proper lubrication is critical to the trouble-free operation and longevity of screening equipment. Users should follow the manufacturer’s instructions and schedules when lubricating bearings, gears and other moving parts. Regular lubrication prevents friction, reduces wear and minimises the risk of component breakage. Replacing components is another important part of maintenance. Worn covers, belts, and other consumable parts must be replaced promptly to maintain optimal screening performance. Keeping spare parts on hand can minimise downtime and ensure a quick response to potential equipment failures.
Calibration and Adjustment
Regular adjustment and calibration of screening plants are necessary to maintain screening efficiency and accurate results. Users should regularly check screen tilt, speed and vibration parameters to ensure they meet desired requirements. Incorrect adjustment can result in suboptimal material separation and reduced performance. In addition, it is important to adjust the screen settings according to the characteristics of the material being processed. Fine-tuning of screen aperture, amplitude and frequency can optimise the screening process and ensure efficient separation of desired size fractions.
Solving common problems
Screening plants can encounter common problems that require trouble to maintain their effectiveness. Problems such as screen glare, material movement, excessive vibration and belt movement can interfere with the effectiveness of the screening process. Operators must be familiar with troubleshooting techniques to identify the root causes of these problems and implement appropriate solutions promptly. This may include adjusting display settings, cleaning or replacing worn parts, or fixing mechanical or electrical problems.
Conclusion
Proper maintenance and troubleshooting are critical for screening plants to ensure optimal performance and minimise downtime. Regular inspection, cleaning, lubrication and replacement of components are essential maintenance operations. Calibration and adjustment help maintain accurate screening, while powerful troubleshooting allows users to quickly solve common problems. By prioritising maintenance and troubleshooting, operators can maximise the life of screening plants, improve screening efficiency and contribute to the overall productivity and success of various industries in India.
View our expansive machinery
With Puzzolana, you have the chance to work with the brightest professionals in the field and be a part of our expanding global footprint. We are looking for motivated professionals to join our team.